Sectorial Need - Automation And Building Remote Working Environment
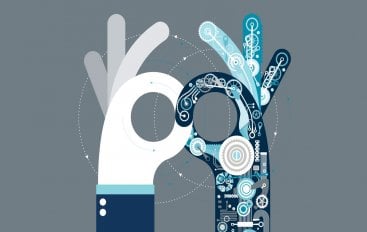
It is still too early to write the history of the 2020 pandemic, but this will likely be remembered as a time when, for many people, the workplace changed forever. Enterprises suddenly got more serious about digital transformation. Automation took on a new and urgent appeal. Remote working and work-from-home became viable alternatives.
With the economy functioning at around 60% of its normal capacity, OEM’s might face the challenges related to non-availability of labor, concerns on health and safety management on the shop-floor, alignment, and rescheduling of projects & programs. The central question remains how can an organization pivot through all these challenges and stay afloat. There are two major factors one should consider:
Always remember People come first:
Safeguarding the workforce’s health should be the top-most priority among businesses. Eaton also used the situation to evaluate several new technologies to see how they could best be used to bolster safety and improve efficiencies. Today, COVID has allowed us to offer flexible work arrangements to the employees. We can train and upskill them on new working methods that involve automation on the factory floors (e.g., moving IT to the cloud). In the long run, these measures will help in reducing operating costs and eliminate maintenance capital.
Work from Home gives the employees autonomy and boosts their morale, ultimately results in increased productivity. The New Normal Working Model fits seamlessly into the concept of the future of work. Concepts like IoT and AI will become extremely relevant as we advance and define the new way of working. Another important practice an organization should follow is working closely with municipal, state, and central governments to coordinate for worker and consumer safety plans while keeping critical productions running.
If your employees work from home and log on to company networks from devices and internet connections that are not fully secure, there are high chances of cyberattacks. For building a safe remote working environment, the organization should prioritize cybersecurity and system resiliency.
Automation in this digitalized world:
In these times when the conventional means and methods of operations are being redefined, it is important to leverage new technologies and integrate them into proven
processes to quickly ramp up operations, while ensuring that quality, cost and performance metrics were met.
As a company, we are exploring accelerated and redefined use of:
· Augmented reality tools
· Additive manufacturing
· Cobots
· Data sharing and analysis
· Digital simulation
OEMs largely depend on supply chain management. Organizations that overhaul their supply chains to better anticipate risks will emerge strongest post-COVID-19. Developing supply chain resiliency includes revisiting the supply chain network design and reconfiguring global and regional supply chain flow suited best during risk scenarios. Companies should deploy technologies—such as transportation management systems, warehouse management systems, robotics and autonomous materials movement—to decrease worker density throughout their operations. Going digital and using technology will not only play a significant role in the supply chain, manufacturing and procurement side but also at the shop floor level. A digitally smart shop-floor design with a focus on planning and execution will become the new normal.
With the accelerating adoption of AI, automation and the rise in new working ways, reskilling will become a priority for many organizations. The crisis has sped up the trend for businesses to embrace remote working quickly. It is more important than ever before to be prepared for transformation. Hence, to maintain resilience for the future, organizations should adopt an agile approach to strategic workforce planning.